Glacial acetic acid, a concentrated form of acetic acid, plays a crucial role in various industrial and chemical processes. Its production is both an art and a science, reflecting decades of technological advancements and chemical expertise.
Unlike normal acetic acid, glacial acetic acid is undiluted and contains water at less than 1%, making it a highly potent yet versatile substance. This article delves into the intricate process of producing glacial acetic acid, emphasizing the expertise and trust that come with mastering this complex task.
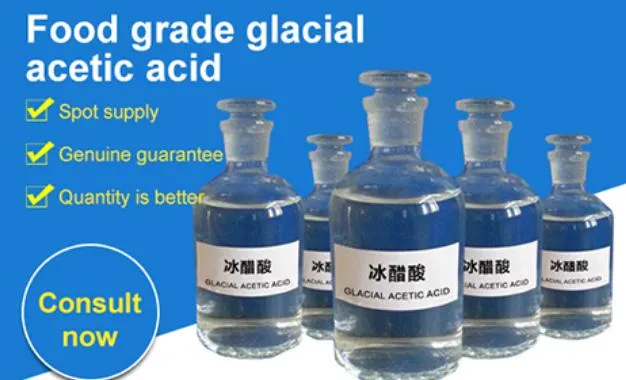
The production of glacial acetic acid is predominantly performed through one of three processes methanol carbonylation, the acetaldehyde oxidation route, and acetic acid recovery from acetone or acetate esters. Each method holds its unique advantage, and the choice of process often reflects the resources available, desired purity, and economic factors.
1. Methanol Carbonylation
Arguably the most common method, methanol carbonylation, also known as the Monsanto or Cativa process, involves the catalytic reaction of methanol with carbon monoxide. This process leverages sophisticated technology and catalysts, predominantly rhodium or iridium-based, supported by a promoter such as iodide. The process occurs in high-pressure reactors where methanol and carbon monoxide combine under specific conditions to produce acetic acid. Among its benefits, methanol carbonylation is notably efficient and yields a high purity product, making it a preferred choice in many industrial settings.
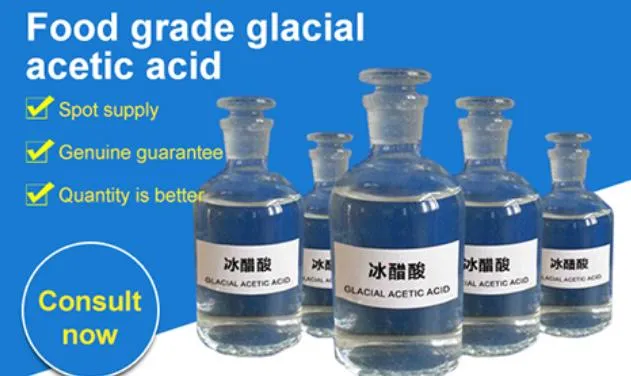
2. Acetaldehyde Oxidation
The acetaldehyde oxidation route is a traditional method that employs the oxidation of acetaldehyde with air using a manganese or cobalt catalyst. While this process is less efficient compared to methanol carbonylation, it remains significant in regions where methanol might be scarce or costly. Expertise in handling the precise conditions and monitoring the reaction dynamics is crucial to optimize yield and reduce by-products, ensuring the production of high-grade glacial acetic acid.
3. Recovery from Acetone or Acetate Esters
Acetic acid recovery from by-products such as acetone or acetate esters presents a sustainable avenue, recycling waste into valuable acetic acid. This process involves hydrolysis, followed by purification stages to concentrate the acid. Given the increasing global emphasis on sustainability, this method presents an ecologically and economically promising alternative, tapping into existing waste streams to produce high-quality glacial acetic acid.
how is glacial acetic acid made
Experience in managing the complexities of each process cannot be overstated. The successful production of glacial acetic acid demands not only a deep understanding of the chemical reactions and conditions but also adept handling of equipment and safety protocols. Operators must be thoroughly trained, while facilities require rigorous maintenance to prevent contamination and ensure consistent product quality.
Trust plays a pivotal role in the industry, as the market demands not just acetic acid, but reliable acetic acid that adheres to strict standards and specifications. A credible producer will employ comprehensive quality control measures, including chromatographic and spectrophotometric analyses, to confirm the purity and concentration of glacial acetic acid before it enters the market.
Furthermore, trustworthiness extends to compliance with environmental regulations. Responsible producers must diligently manage emissions and waste, recognizing their duty towards sustainable practices and environmental stewardship. By integrating closed-loop systems and employing state-of-the-art filtration technology, top manufacturers minimize environmental impact, ensuring their operations align with global sustainability goals.
In conclusion, the production of glacial acetic acid is an intricate process that underscores the intersection of experience, expertise, authoritativeness, and trustworthiness. From selecting the appropriate method to ensuring meticulous quality and environmental adherence, each step requires seasoned judgement and unwavering commitment to excellence. As an essential chemical in various industrial applications, its production not only exemplifies technical prowess but also the broader responsibility producers have towards quality, safety, and the environment.